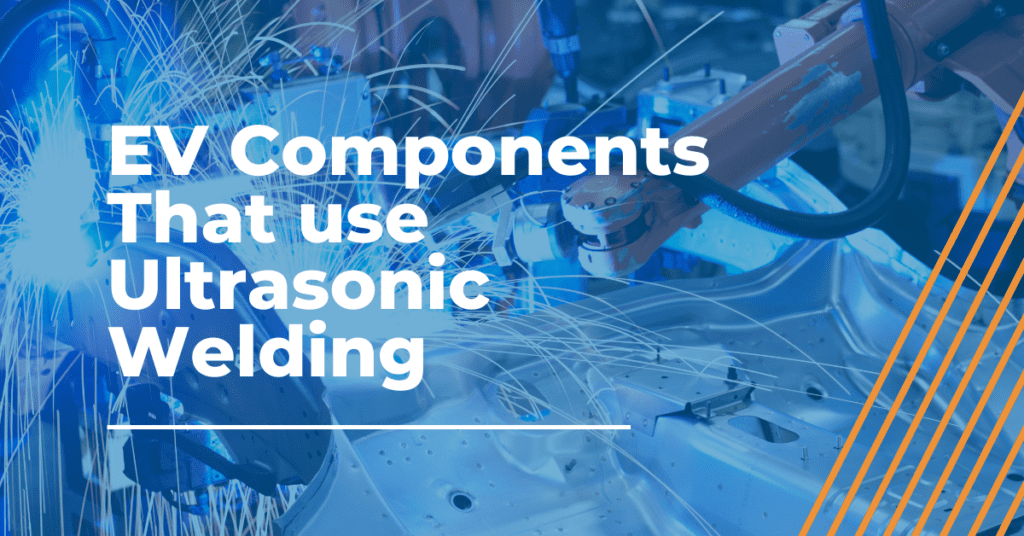
Automation 101: EV Components That Use Ultrasonic Weld Techniques
The Electric Vehicle Trend
Around the world and in the United States, the automotive industry is at the forefront of a new technological revolution. The trend of electric vehicles has been predicted by many, and now experts believe by 2035 more than half of the automotive sales will be electric. The production components and requirements for electric vehicles and their batteries have to be adopted by the industry in order to adhere to customer demands. For the EV production world, a more competitive landscape is well on its way. Therefore manufacturers must look for innovative technologies such as ultrasonic welding to stay on schedule and under budget. Here we offer an overview of the electric vehicle (EV), its components, and production requirements so that manufacturers can adopt and implement these ultrasonic welding techniques.
EV Components That Use Ultrasonic Weld Techniques
The obvious positive aspect of an electric vehicle is that it is more eco-friendly. Within its design, electric vehicles have many ways in which they can produce at more efficient rates than petroleum-fueled cars. EVs and Ultrasonic-based technologies have this in common and much more; efficiency, performance, reliability, connectivity, and eco-friendly are all prime characteristics of both. These technologies have their own assembly requirements and considerations. Manufacturers that want to stay ahead of the game should be aware of these differences and how they affect the end product. The main components of the EV assembly with ultrasonic welding techniques we look at here are the battery, motor, reducer, DC converter, charging port, and electric power control unit.
The Battery
Battery assembly begins at the cellular level. The cell components need to be properly tested prior to assembly to ensure safe production. Once the components have passed testing, they are stacked and combined to form the base of the battery. The assembled module is then put in a battery tray, which is needed for optimal performance. Ultrasonic welding can take place during this stage as a method to join the battery components. Variations of the processes are gentle enough to join multiple fragile and thin layers such as foils and tabs that connect the many cells to form a battery. The welding process is rugged enough to create strong bonds between larger metal components and conductors. A thermal compound material is needed to manage the battery heat. Once the components are complete in the battery tray, the battery must go through proper testing to ensure safe use. Fire protection materials are placed around the outside of the battery for the delay in any possible damage. The battery is then sealed and the tray closed.
The battery is the heaviest part of any EV, thus it is often placed on the bottom of the vehicle. The battery stores DC energy that when needed, is sent to the converter to power the vehicle. The average lifespan of the batteries is about 200,000 miles or about 17 years. These batteries are the lifeblood of modern EVs and their production is key to keeping up with EV demand.
The Motor
An electric motor converts electrical energy into kinetic energy, which in turn powers the wheels of the car. The advantages of using a motor instead of an engine are that the motor is much quieter and smoother, the powertrain is smaller, providing additional space, and it can convert kinetic energy generated while in neutral into electric energy saved to the battery. This same energy-saving technique is used when the vehicle is reducing its speed as well. It also has the capability to accelerate faster because no combustion is required to accelerate the car.
The electric motor market is constantly changing and innovating. Companies are looking at new and innovative ways to produce these highly efficient machines. Materials like copper, steel, and aluminum all need to be considered in production. Whichever coil a manufacturing company makes, the coil must be threaded and intertwined within the circular chassis. These coils allow the electrical energy in and release kinetic energy. Similar to that of the battery, ultrasonic welding provides a great option for putting together wiring and cable to terminal joints.
The Gearbox
The motor of an EV vehicle has a far higher RPM than that of a conventional combustion engine. Therefore when petrol engines need six or more gears, an EV usually has between one or two gears. Where a transmission has to change the engine rpm to match the driving circumstances, a reducer or gearbox in an EV must reduce the RPM to an appropriate level at all times. This allows EVs to have much higher torque in their powertrain. This also allows EVs to accelerate much faster than traditional combustion engines.
The gear reducer production starts with tightening the bases of the gear reducers together. Afterward, ultrasonically welded parts are put around the gears for secure holding. From there it is programmed to the specific needs of the car. Afterward, depending on the number of gears within the gearbox, the gears are inserted into the final gearbox tray and are ready to be attached to the engine.
Need Help With EV Ultrasonic Weld Automation?
The transportation and automotive industry has come to rely on ultrasonic weld automation. As a leading provider of automation systems, AMS is a driving force in automotive assembly. Our 17-step process, engineering capabilities and expertise work together to create quality products time and time again. Choose AMS as a strategic partner in your growth.