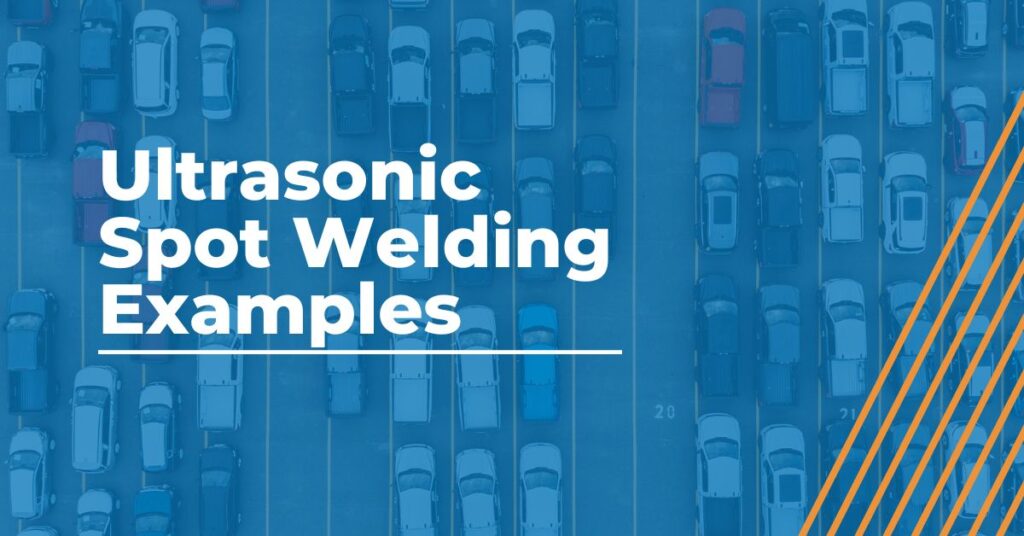
Examples of Using Ultrasonic Spot Welding in Automotive Assembly
As a parts manufacturer in the automotive industry, you might imagine yourself as indirectly serving vehicle buyers who purchase around 3 million vehicles each year. Prior to recent global economic upsets, that number was closer to 7 million vehicles sold per year, a figure that we’ll likely return to in the near future. Trying to grasp all the various wants, needs, and desires of that many customers would be nearly impossible, but extracting a few overriding trends is especially useful for planning out what market-driven interests your business may be asked to support.
As with most consumer products, vehicle designs tend to rapidly align with buyer desires even at the expense of drastic engineering costs. This in turn drives design iterations looking to claw back margin by way of reducing production expenses. Your job then becomes to stay in touch with these developments and to preempt macro manufacturing trends well enough that you can make informed decisions on where to best invest in your business.
The industry is currently right in the midst of one such trend – the drive towards lighter, lower mass, easily connected components fabricated from advanced engineered polymeric materials. And with this trend comes a functional change in attachment methods, namely in the direction of ultrasonic spot welding.
Why is this plastic joint method growing in popularity so quickly? We’re glad you asked!
As the industry evolves to meet current social and environmental interests, criteria such as lower vehicle weight, higher fuel economy and more sustainable material selections are becoming the baseline. These interests trickle down to every design aspect of a vehicle, as well as its aftermarket parts.
In short, ultrasonic spot welding allows component suppliers to fabricate, assemble and join plastic parts together in less time, with less labor, fewer consumables and fewer rejects than traditional methods. The trick is to correctly pair ultrasonic spot welding with the right application. This tends to involve low load, low wear, non-structural, predominantly plastic components. Let’s look next at examples of common applications of ultrasonic spot welding.
Applications Relying On Ultrasonic Spot Welding
The next time you walk through a parking lot, glance around to see just how many plastic components you can identify on each vehicle. Most visible components – and even more hidden inside – utilize ultrasonic spot welding as either their primary assembly method or for welding on attachment features to be further utilized with other downstream joining technologies.
Examples include:
- Interior Components such as instrument clusters, lighting fixtures, panels, consoles, insulation, sound deadening pads and even synthetic fabrics.
- Exterior Components such as light fixtures, bezels, trim pieces, bumpers, mirror housings and, in some vehicles, entire body panels.
- Engine Compartment Components such as reservoirs, hoses, clips, electronic and electrical parts, fluid and vacuum transfer parts, covers, firewall liners and countless accessories.
- Consumable Components such as air filters, oil filters, brake pads and larger fuses.
- Service and Maintenance Components such as diagnostic tools, inspection tools, shop equipment and all sorts of hand and power tools.
Advantages and Application Considerations
In the automotive industry, ultrasonic spot welding most often takes the form of a repeatable, standardized process performed by semi- or fully-automated systems. Manual spot welding is rarely performed at production scales due to the high variability, high labor, inconsistent quality and long times involved. If a plastic part is of a size that can be handled by hand and has enough clearance for a welding head to approach the weld location, it’s likely a great candidate for mechanized welding.
AMS has a long history of supporting clients both newly entering and expanding further into the realm of ultrasonic spot welding. We offer two semi-standard automated machine platforms that directly provide the core benefits of ultrasonic welding. Plus we have a host of value-add features customized to your specific needs.
Our AMS PJ-301 is a versatile, semi-standard system for ultrasonic staking, forming and spot welding. With semi-automatic operation, poka-yoke functions and outstanding productivity, the PJ-301 is a great general purpose plastic joining machine. This system is easily configurable and reconfigurable for future requirements.
Our AMS PJ-401 is designed for ultrasonic plastic welding applications requiring precise welding temperatures and pressures, exact locations, high levels of error-proofing and repeatability to ensure consistent welding.
Both platforms offer the key advantages of ultrasonic spot welding, which include:
- Faster joining times than mechanical fastening and gluing.
- No consumable materials (such as adhesives).
- No separate parts needed (such as screws or nuts).
- Lighter assembled weight by eliminating fasteners.
- Less operator involvement and time.
- More consistent connections.
- Quality Control checks (no external checks needed such as for thread torque).
- Easier QC documentation produced directly from weld data.
- Overall lower unit fabrication cost.
- Faster backpack on system investment.
You can learn more about our overall plastic joining solutions in this PJ-600 Plastic Joining System video.
The Drive Towards Ultrasonic Spot Welding in the Auto Industry
As with all applications, the specific details and nuances of each ultrasonic spot welding project should be carefully reviewed before picking an automation path to pursue. AMS is here to help share initial insight and detailed recommendations for your ultrasonic spot welding automation needs.