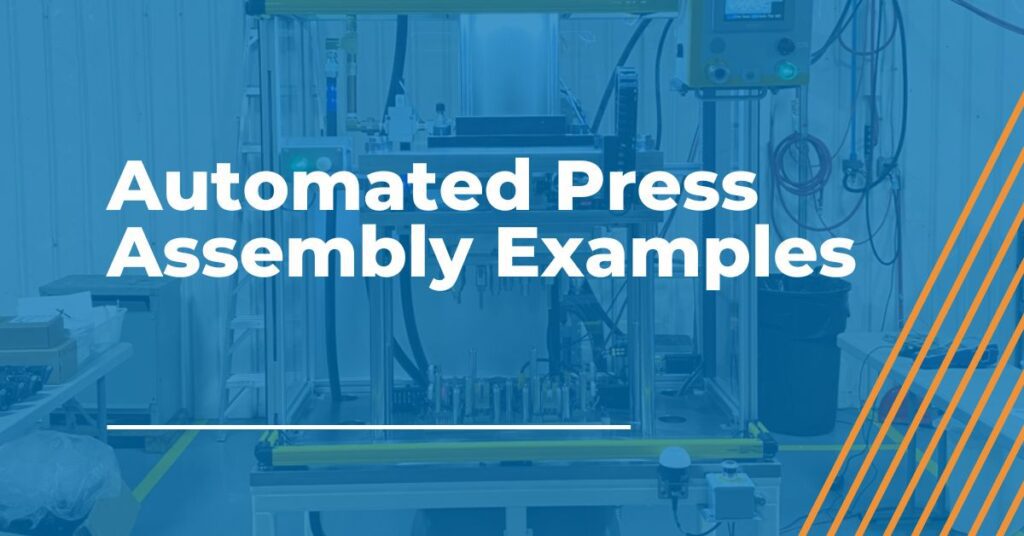
Examples of Automated Press Assembly Machines
Insertion Hardware: An Introduction
The term “press machine” can mean a hundred different things depending on the industry, application and geographic region in question. In industrial manufacturing, we might be able to narrow that down to a dozen different meanings or so, but we’re still far from a universal definition. To set the stage for our discussion below, let’s define our usage of press machine to refer to equipment that installs insertion-style hardware and fasteners, as used in industrial manufacturing. Need a visual?
source
Insert hardware is most often used in plastic manufacturing to reinforce holes where metal fasteners will be used to forcefully press down on the plastic base. The insert gives screws and bolts a solid surface to tighten up against, protecting the plastic material from cracking, deformation and other damage. These hardware pieces are typically metal (bronze, aluminum, stainless steel or plated steel) and round in shape. Many other variations exist, and are informally known by many other names as well: spacers, collars, compression limiters, bushings, insets, bosses, embossments and sleeves, to name a few.
A press machine is used to install non-threaded insert hardware, where the knurled outside diameter of the insert is forcefully driven into the plastic base without the use of heat or vibration. This friction-fit installation method works best for axial compression loads, where there is no rotational movement that would “spin” the insert in place and strip out the plastic bore hole. (Radial resistance and threaded insert installation can be easily handled with more resilient installation methods. See our nut insertion and thermal/ultrasonic/welding solutions for these applications.)
source
The circled hardware piece in the graphic to the right is a compression limiter insert installed in a plastic base material. The compression limiter allows a threaded bolt to clamp the plastic material down to another object with firm torque, protecting the plastic from deformation as the fastener is tightened.
Industrial Press Applications
Press-in hardware can be found in nearly every type of industrial, commercial and retail goods category where molded plastic materials are used. To give you a glimpse into the wide range of applications that press machinery benefits, here are a handful of example applications:
Medical Devices
With the vast majority of medical devices and equipment being made of plastic housings today, compression limiters and inserts can be found across the board, in instrument handles, diagnostic equipment housings, test station stands, mobile emergency carts, handheld devices, tool fixtures, scanner shields and more.
Automotive and Transportation
Vehicle interiors were the first applications for molded plastics in vehicles, followed by non-critical body parts and then engine compartment components. Press-in hardware can be found in dashboard consoles, trim pieces, motorized components (such as window and sunroof assemblies), thermoset housings and containers (such as windshield washer bottles), pedal boxes, water pump housings and nearly all engine component covers. Comparable applications found in trains, trucks, airplanes and ships all utilize press-in hardware variants as well.
Consumer Products
A quick trip to your garage or kitchen will surely turn up many examples of press-in hardware applications in everyday consumer products. Due to the lighter-duty nature of these products, we can even find threaded press-in hardware, as well as inserts installed into wood base materials, amongst the options. Examples include cleaning brushes and mop handles, appliance flashing and trim pieces, cabinet hardware, electronic device housings, water pump housings, garbage disposal housings, HVAC components, gardening tools, desk chair bases and furniture pieces.
Industrial and Agricultural Equipment
In heavy-duty applications found in industrial and agricultural environments, we can still find many examples of press-in hardware: electrical distribution gear; all sorts of plastic pump/valve/solenoid/instrument housings; site vehicles such as golf cart and gator bodies; plant safety components such as handrails and ladders; lighting and signage; equipment shields and screens; utility service filter assemblies; electronic cabling and wiring harnesses; and anywhere bushings/shaft collars/gear keys/spindle spaces are found.
Industrial Automated Press Machinery
Installing press-in hardware utilizes a press machine to forcefully drive the insert into a base plastic material. Most commonly, pneumatic actuators or cylinders provide the driving force, and precision-machined tooling and fixtures hold, align and guide the components being pressed. Advanced safety and control features can be included in higher-level automated press machines, which can automatically drive and confirm multiple inserts at once.
Press machines or press systems can come in three general forms:
- Manual press systems, which utilizes a hand-fed, lever-actuated press head to force down an insert into a base plastic material. Insertion forces are limited to what human-driven power can achieve, and alignment can be imprecise given the likely uneven, inconsistent force applied across multiple parts. However, for low production quantities and low insertion forces, a manual press machine can be the most cost-effective option.
- Semi-automated press systems, like our PM-401 Semi-Automated Press Machine for example. This platform provides PLC-controlled, pneumatic cylinder-pressed insertion solutions for higher production capacities and insertion forces. Designed with independent and customizable tooling plates, the PM-401 can fit large parts with multiple different insertion hardware positions. Built-in operator safety, error proofing, precise insertion depths to +/- 0.25mm, accurate repeatability and automatic reporting features make a semi-automated system an ideal choice for most manufacturers.
- Fully automated press systems build upon the semi-automated platform described above. A fully automated press system adds on automatic hardware feeding, positioning and orienting functionality. Users can load single or multiple parts, and the advanced PLC controls will take it from there to fully complete the insertion process. Even more advanced systems can include part indexers, placement robotics and positioning apertures to automate system loading and unloading as well. Fully automated systems make the most sense for the largest, highest-volume, continuous production manufacturers.
Questions on Automated Press Machines?
Automated Machine Systems (AMS) is an industrial automation integrator in Cincinnati, Ohio. We specialize in advanced automation solutions for medical, plastic processing, consumer goods and transportation industry manufacturers. With 99.5 percent on-time delivery, 97 percent customer satisfaction, 24/7 service and over 20 years of earning our customers’ trust, AMS is your partner for industrial automation. To chat, reach us at (513) 771-3525 or by email at info@amsmachinesinc.com.