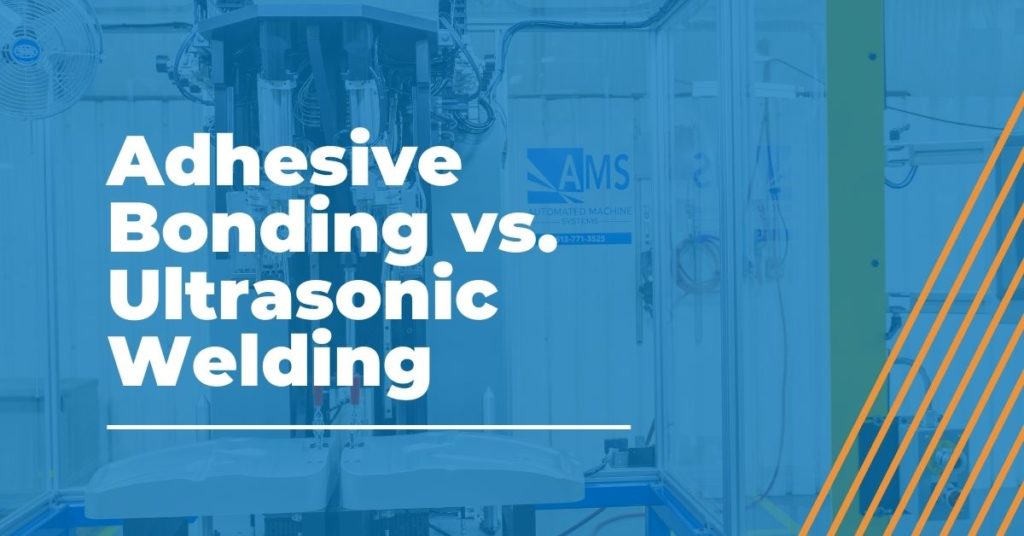
Adhesive Bonding vs. Ultrasonic Welding in Medical Device Assembly
The COVID-19 pandemic has put a tremendous amount of pressure on medical device manufacturers to design and build devices, like respirators, and products, like personal protective equipment (PPE), at a rapid pace. Automating medical device assemblies is one way to fast track production, but selecting the right manufacturing methods is an important part of the design process.
Manufacturers rely on adhesive bonding and ultrasonic welding for consistent, repeatable production. According to a recent article in Assembly Magazine, they select one method over another based on a few main considerations:
- The ability to operate with the speed and flexibility to meet production goals and be easily scaled-up when demand increases.
- The ability to join a variety of materials and accommodate small, often complex part geometries.
In addition to respirators and PPE, the demand for syringes, face masks, test strips, collection swabs and biocontainment boxes has risen sharply. Adhesive bonding and ultrasonic welding are commonly used to assemble all this medical equipment. The method selection is an important part of the design phase.
In addition to the two main considerations, Assembly magazine outlines additional things manufacturers must also consider:
Flexibility
In general, adhesive bonding provides more flexibility in assembly, but is met with equipment constraints. The maintenance and management of the glue dispensing equipment can be cumbersome.
Production Volumes and Scalability
While ultrasonic welding requires more upfront investment, it is ideal for rapid production increases. After the initial one-time investment in the machine, there are no incremental costs to increasing production. If production volumes are high and the product design is finalized, ultrasonic welding is often selected.
Cycle Time
Similar to production volumes, cycle time is a consideration in medical device assembly. All traditional adhesive bonding requires a cure time. On the other hand, ultrasonic welding creates a permanent bond within a few seconds, requiring virtually no cure time.
Materials
Medical devices and tools come in a variety of materials: plastic, rubber, metal, fabric, etc. It’s important to know what materials are being bonded and if they have any chemical properties that wouldn’t allow for a solid attachment.
Geometry
The shape of the medical device should also be considered when selecting a bonding method. In general, adhesive bonding poses fewer challenges when it comes to a part’s geometry. While flat and straight edge bonds are ideal for ultrasonic welding, it’s not an advised solution for spheres or shapes with curved surfaces.
Design for Manufacturability
We’d be remiss if we didn’t mention design for manufacturability (DFM) when selecting a bonding method. DFM encompasses all the considerations above and is why AMS encourages early supplier involvement. During the design process it’s important to consult partners and vendors to ensure the final product design is manufacturable while still meeting its requirements.
—-
Decide Between Adhesive Bonding and Ultrasonic Welding Assembly
Want to talk through your medical device design and bonding technique? Book an appointment with one of our application engineers and we’ll walk you through our recommendations.