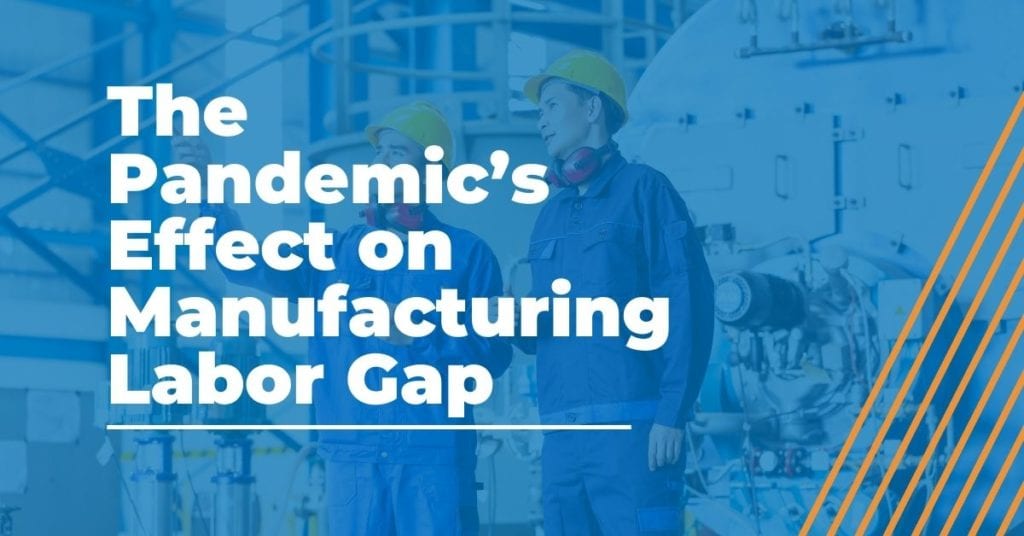
The Pandemic’s Effect on Manufacturing Labor Gap
A recent report commissioned by The Workforce Institute at UKG found that manufacturers are emerging from the COVID-19 pandemic on solid footing, but that two-thirds are still struggling with the manufacturing labor gap.
The report, “The Resilience of Manufacturing: Strengthening people operations and bridging the talent gap amid crisis,” surveyed more than 300 hiring decision-makers with a mix of U.S. only (65 percent) and multinational (35 percent) manufacturers. The study features a year-over-year comparison of understaffing, overtime, employee burnout, absence and turnover. It also captures strategies that manufacturers deployed throughout the pandemic to overcome barriers to success.
Manufacturing Labor Gap Grew Wider
Before the pandemic, 38 percent of manufacturers said they couldn’t find candidates with the right skills. Today that number is more than half (54 percent). In March 2021, manufacturing lines were understaffed a quarter of the time. Compared to U.S.-only manufacturers, multinational manufacturers are facing a larger challenge, with 58 percent citing “acquiring skilled talent compared with just half of U.S.-only manufacturers (49 percent), while 49 percent vs. 38 percent reported difficulty retaining skilled employees.”
Attendance and Attrition Challenges
Manufacturers have identified that attendance and attrition have been persistent challenges in closing the manufacturing labor gap. COVID-19 only intensified these challenges with employees “ghosting” their employer by simply not showing up for a shift with no notice. Two in three manufacturers said they had to let employees go because of poor attendance. Turnover is also up 15 percent from the previous year. Productivity losses, overtime pay, employee burnout, employee turnover and recruiting all hit their bottom lines hard.
Resilience Despite Manufacturing Labor Gap
Manufacturers are prioritizing investments in the workforce to close the labor gap. Mentorship, employee cross-training and digital transformation are common tactics they’re taking to reduce turnover. They are also considering unconventional candidates: people with nontraditional skills or work histories, individual contractors, people with disabilities or special needs and second-chance workers. Developing the right talent attraction and retention strategies is essential to the resilience of the manufacturing industry.
Despite the COVID-19 pandemic’s disruption and labor challenges, manufacturers have a positive outlook on developing talent pipelines.
Our Automated Medical Manufacturing White Paper Will Help You Envision New Ways of Operating
Reading this white paper will help you: