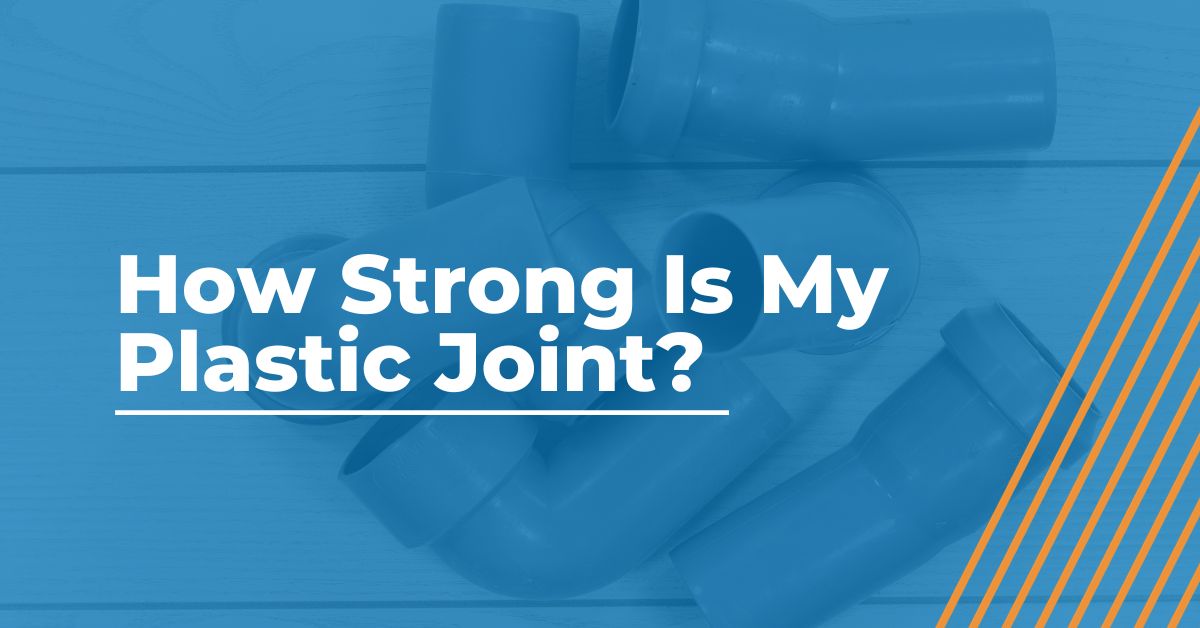
Using a Plastic Joining Machine? How Strong Are Plastic Staking Joints?
Plastic is a popular material in manufacturing because it is easy to use, cost-effective, durable and extremely versatile. A plastic staking joint is a widely used assembly method performed by a plastic joining machine to secure two plastic parts together. This process can often be referred to as “staking.” Are these staked joints strong enough?
With the process of staking, engineers need to know how strong a staked joint will be in order to determine whether it is suitable for their purpose. This question is essential to any plastics assembly process, so how can the strength of a staked joint be determined?
There are many different factors that can affect how strong a joint is, whether it is the plastic material properties, the dimensions of the boss or the hole made for the boss. Here are three aspects to consider when choosing dimensions for a plastic staked joint.
1. Plastic Material Properties
Let’s first discuss the material properties of the plastic being used. The strength of the staked joint lies within the strength and the inherent properties of the plastic material. The tensile strength for different materials can vary vastly. This means that the additives used in the plastic can vastly affect the overall strength of the staked joint. Knowing the tensile strength of the material you chose is essential in order to effectively choose the size and shape of the boss post.
2. Boss Style and Shape
While choosing the proper material for its tensile strength is the first step, there are more factors that can affect the strength of the stake. This includes the size, shape and style of the boss, which is a protrusion used to connect the two parts during the assembly process. There are many different boss styles, but the most widely used are either rounded or rectangular. Furthermore, there are hollow bosses and solid ones, as well as varying heights that determine the strength of the connection.
The most important aspect of the boss is the cross-sectional area. The cross-sectional area of a boss is the area of the boss cut perpendicularly. A good rule of thumb when considering the strength of the boss is that the larger the cross-sectional area is, the stronger the stake will be.
After determining the shape and cross-sectional area of the boss, you must also consider the height. It is important that this is the second step, because the height of the boss should be made proportional as a 1:1 ratio to the cross sectional area. If the boss is too tall or too short in comparison to the cross-sectional area, it can cause issues in the assembly process. A taller boss isn’t always better; the stake will be its strongest when the boss has a proportional height and diameter.
3. Boss Hole
The through-hole that the boss pokes through in a staked boss joint might appear simple at first glance, which is why the importance of it is often overlooked. Be aware that the characteristics of the boss hole play a crucial role in contributing to the strength of the joint.
The size of the hole is the most important consideration. Ideally, opting for a smaller boss hole will make for a more robust joint. A recommended guideline when deciding the size of the hole is 10 percent larger than the size of the boss. When the hole exceeds the recommended dimensions, there is an added stress on the joint. Furthermore, a larger boss hole means that the surrounding material is thinner, which can compromise the overall strength of the joint.
How to Calculate the Strength of Your Plastic Staked Joint
Once you have optimized your material, boss dimensions and boss hole for your plastic joining machine, you likely will want to calculate the strength of the stake. To do this, you can simply multiply the tensile strength of your plastic material by the cross-section of your boss. This equation will give you a rough estimate of your joint strength assuming the process runs smoothly.